Как делают вертолеты в Казани (48 фото)
История Казанского вертолетного завода берет начало в 1933 году, когда на берегу Волги в Казани было основано производство по обработке дерева. А сам завод свою историю исчисляет с 4 сентября 1940 г., когда приказом Наркомата авиапрома был создан ленинградский авиационный завод № 387, который позднее эвакуировался в Казань и объединился с заводом обозных деталей №169.
Авиационная судьба предприятия была определена в 1940 г., именно с этой даты идет отсчет истории нынешнего ОАО «Казанский вертолётный завод». В 1941 году легкие бипланы стали первыми воздушными судами, выпущенными заводом.
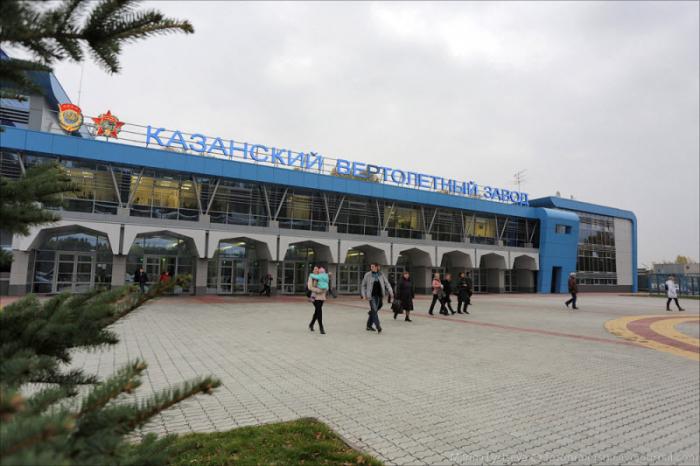
В 1956 году Казанский вертолетный завод начал поставки вертолетов на экспорт.
В 1965 году началось производство вертолета Ми-8. Это стало поворотной точкой в истории завода. Современный вертолет Ми-17 и его модификации - это результат огромного опыта, накопленного за время производства и эксплуатации вертолетов Ми-8.
Казанское вертолетное производственное объединение в 1993 г. преобразовалось в акционерное общество Казанский вертолетный завод, а в 1996 г. стало открытым – ОАО «Казанский вертолетный завод»
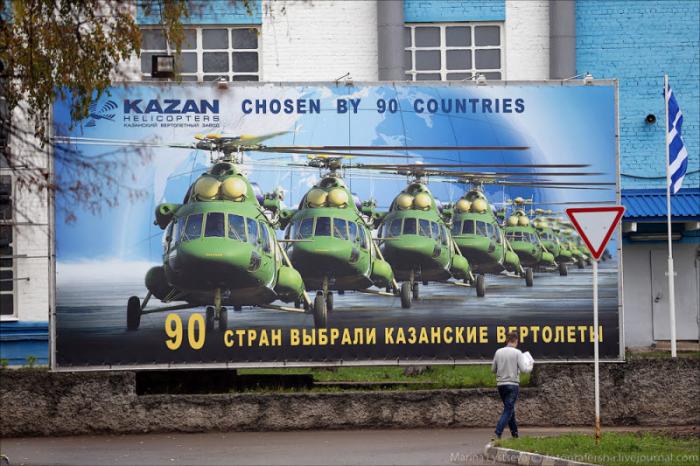
Производство вертолетов:
2006 - 53
2007 - 38
2008 - 58
2009 - 67
2010 - 81
2011 - 94
2012 - 103
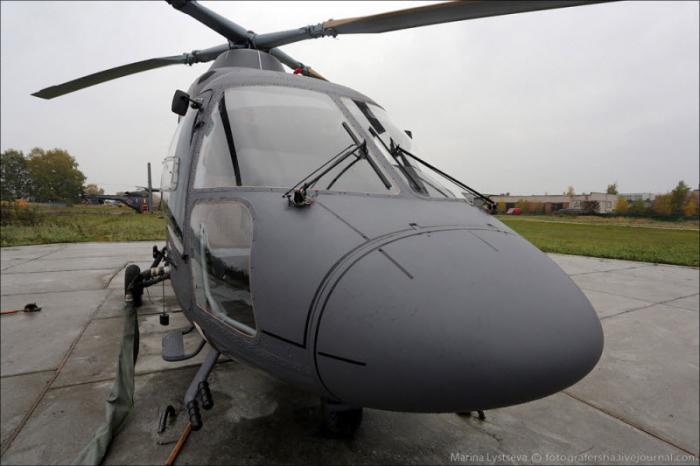
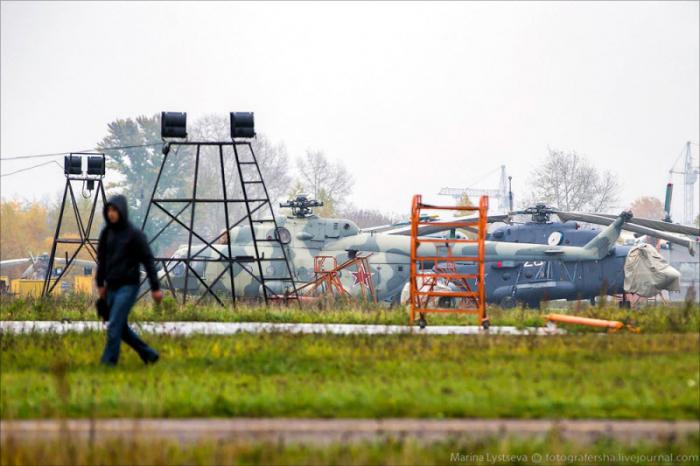
На сегодняшний день КВЗ остается самым большим в мире производителем вертолетов среднего класса.
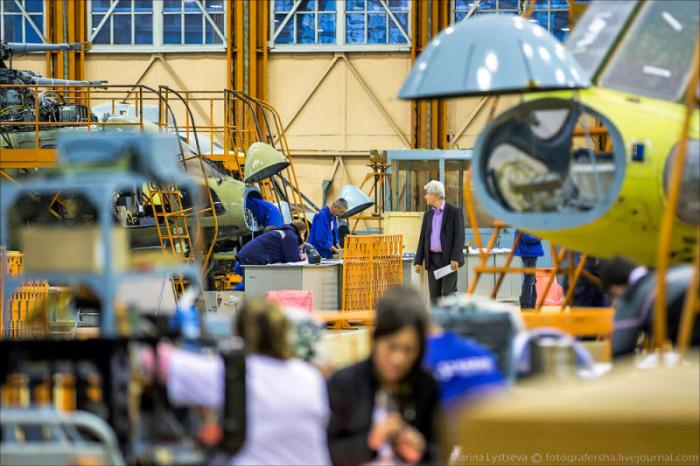
Традиционные для российского вертолетостроения рынки: Россия, страны СНГ, государства Юго-Восточной Азии, Африки, Центральной и Южной Америки. В настоящее время КВЗ поставляет технику примерно в 90 стран мира (продукция холдинга "Вертолетов России" в целом представлена более чем в 110 странах мира).
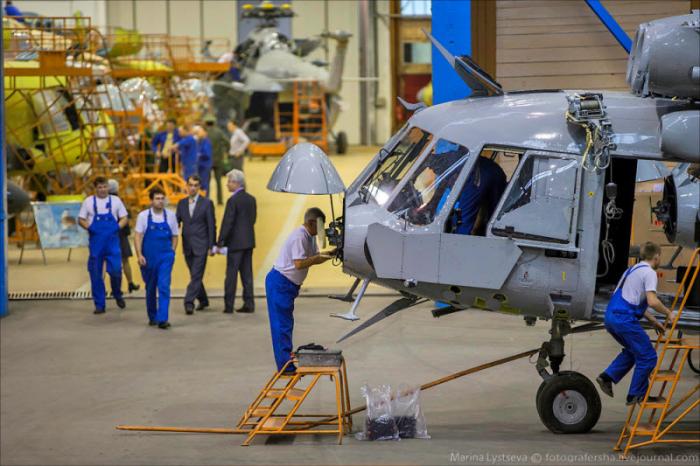
В этом году планируется достигнуть уровня свыше 100 машин в год при почти не изменившемся составе рабочего коллектива - около 7 тысяч человек со средним возрастом 36 лет (в цехах механического производства; по заводу средний возраст на сегодня – 43,2 года). И достигнуто это за счет реорганизации производства, которая началась в начале 2000-х годов с ремонта цехов.
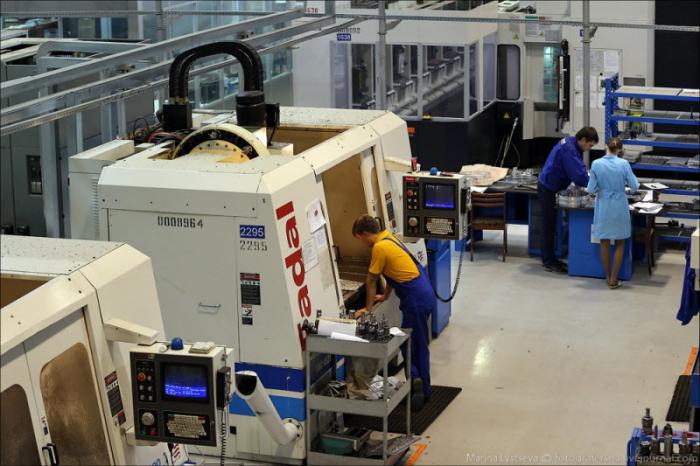
Не менее важный этап реорганизации предприятия последовал с закупкой нового оборудования в механообрабатывающее производство. Закупили станки иностранного производства, в связи с чем трудоемкость упала, а производительность труда выросла в 4 раза.
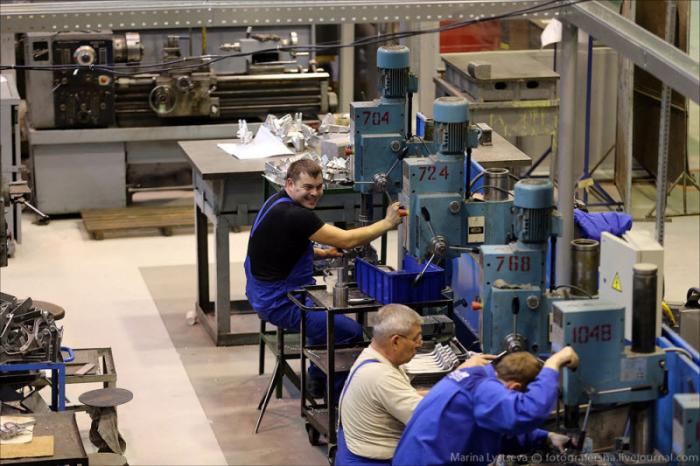
Шпангоуты сейчас обрабатываются на четырех трех- и пяти - координатных станках, которые заменили 24 старых (три линии по 8 станков каждая). Россия, к сожалению, пока не выпускает станков такого уровня. На фото – обработанная штамповка до покрытия.
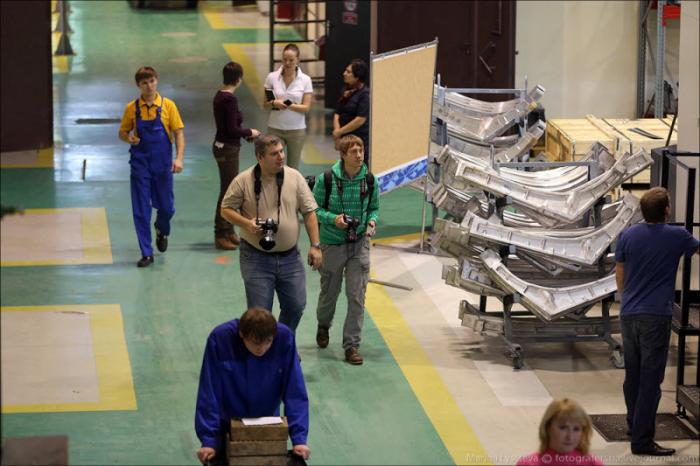
Готовые шпангоуты идут на дальнейшую сборку.
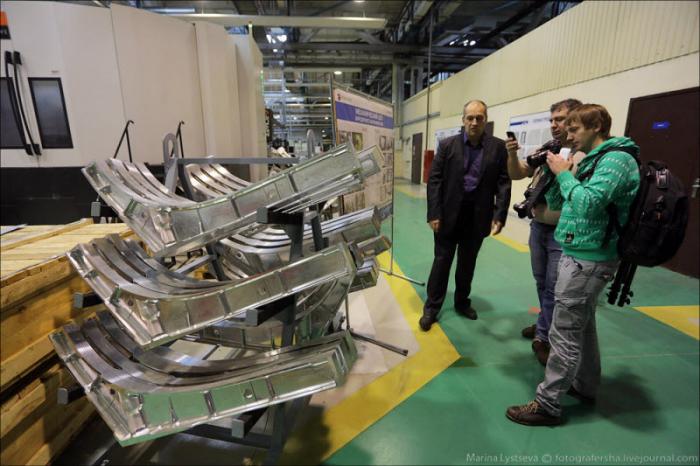
Деталь для автомата перекоса для "Ансата" раньше изготавливалась за 18 часов, а сейчас 12. Из-за обработки на нескольких станках брак составлял большой процент. Сейчас вся токарная часть, фрезеровка, сверловка осуществляются в рамках одного цикла. И так происходит со многими деталями.
На фото кольцевой шпангоут, который идёт на хвостовую балку на серийный вертолёт.
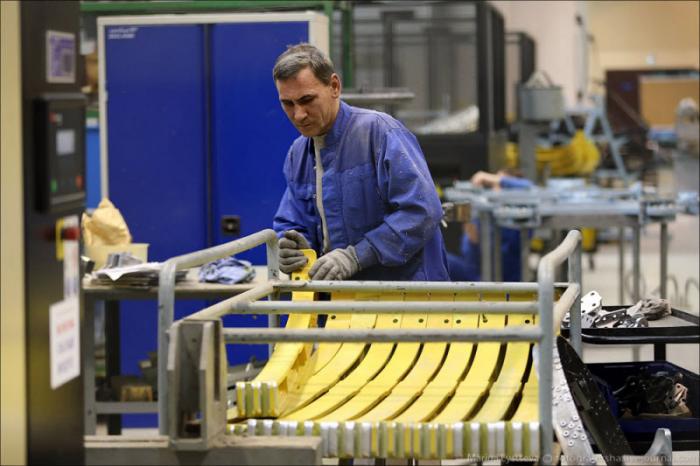
Ступица виброгасителя. Не каждый клиент ее заказывает. Раньше на изготовление этой ступицы уходило 136 часов, сейчас 18 - время сократилось почти в восемь раз!
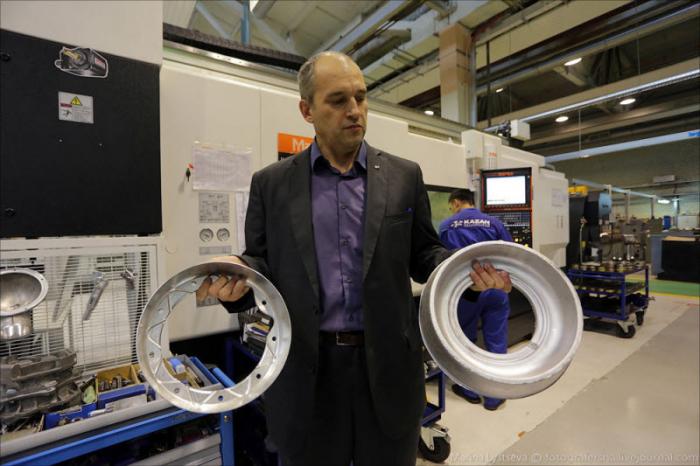
Служба главного технолога находится тут же в цеху за стеклянной перегородкой и не нужно ждать подолгу, как раньше, специалиста, пока он прибудет из другого корпуса.
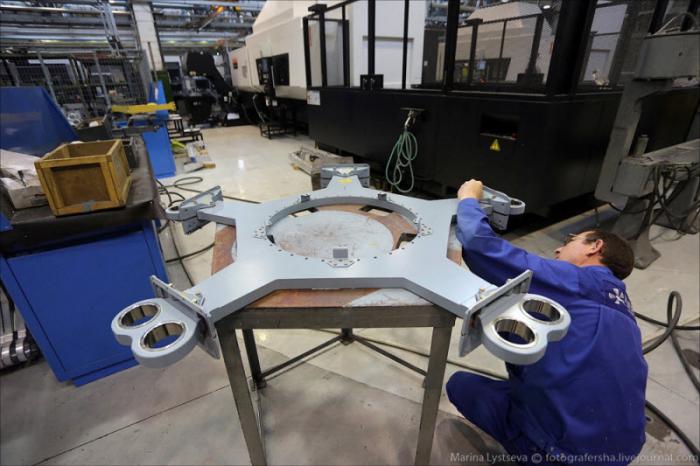
В цехе фрезерного направления работает 2 линии фирмы «Mazak». Одна (4 станка) обрабатывает легкие сплавы (дюраль), другая (3 станка) только сталь. Каждый станок имеет свой магазин на 120 инструментов, а на «стальной» линии ещё и магазинный центр на 240 единиц. Замена инструмента на «стальной» линии формируется автоматически – это заложено программным обеспечением.
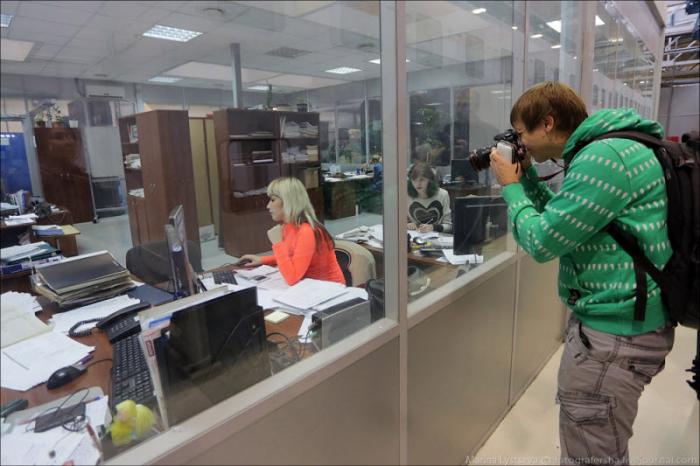
Допустим, у фрезы закончился ресурс, компьютерная программа сигнализирует о завершении назначенного ресурса, бегающая каретка забирает фрезу со станка, производит обмен и идет дальнейшая обработка детали. А оператор забирает отработавшую своё фрезу. Инструмент идет на переточку, его характеристики меняются и он идет на другое производство. Все инструменты с чипами, на которых записана история жизни детали.
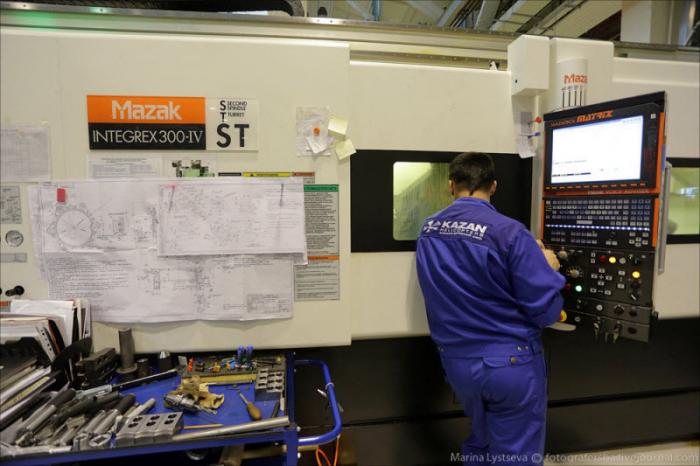
За время перестройки этот цех увеличил свою мощность более чем в три раза. Если раньше делали 6 тысяч нормо-часов, то сейчас план подходит к 21 тысяче, а с января 2014 будет ещё больше.
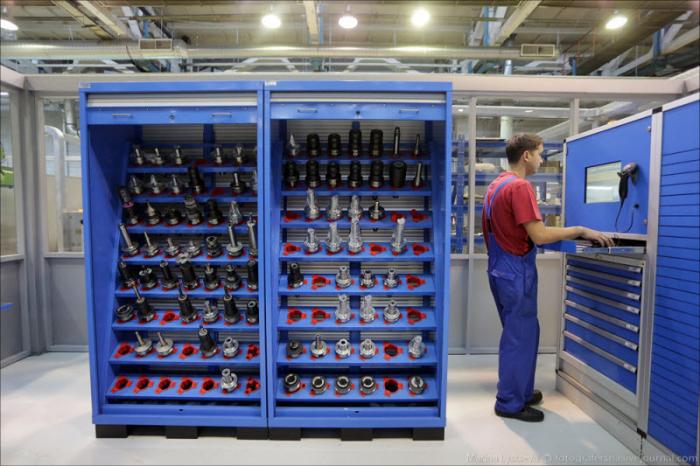
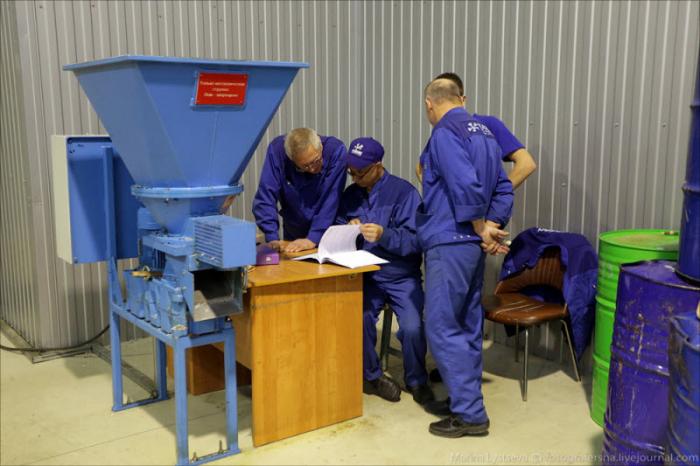
Раньше каждый день отсюда уходил груженый самосвал дюралевой стружки, сейчас отходов стало в 4 раза больше, но стружка превращается в удобные для транспортировки брикеты, которые после переплавки идут в другие виды промышленности.
Каждые 28 секунд из пресса выпадает дюралевый брикет. Каждые 32 секунды – стальной. Стоимость брикетов на рынке в 4-5 раз больше, чем просто стружка. Витую стружку утрамбовщик в брикеты делать не может, поэтому она попадает в «мясорубку» и после измельчения тоже занимает меньше места.
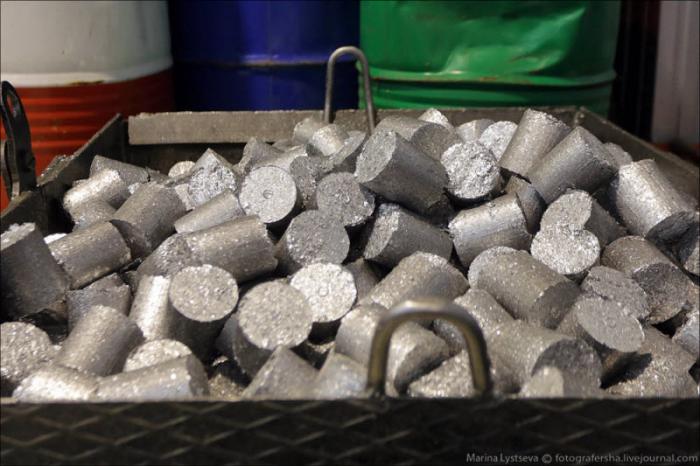
Экологическая защита. На заводе не водятся крысы и мыши. Репортаж Алексея смотреть у него на страничке.
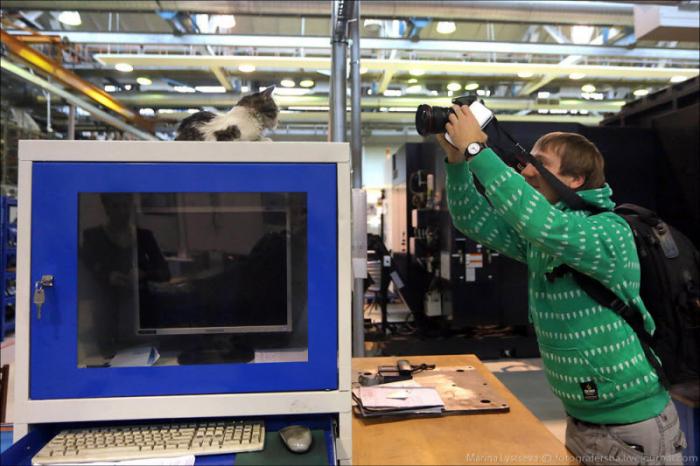
Чистота - залог экономического роста производства.
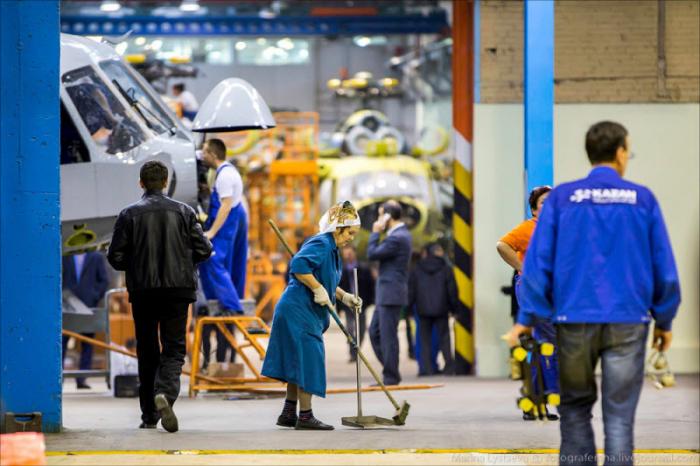
Перемещаемся в сборочный цех.
От начала сборки до первого полета вертолет находится тут в среднем один месяц, включая малярное производство.
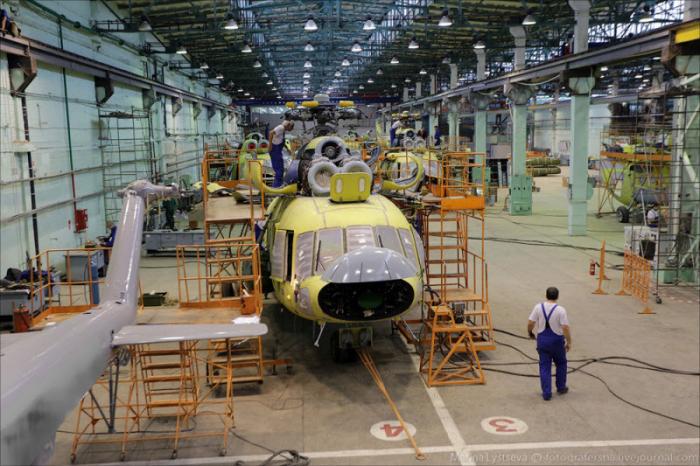
ОАО "Казанский вертолетный завод", входящий в холдинг "Вертолеты России", производит семейство вертолётов Ми-8/17, которые эксплуатируются более чем в 100 странах мира
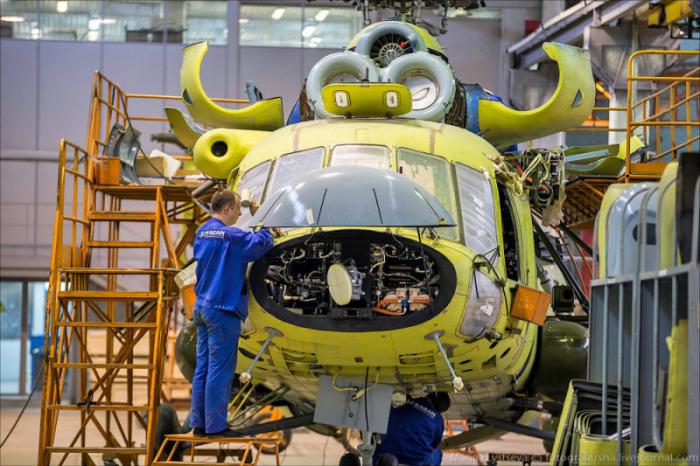
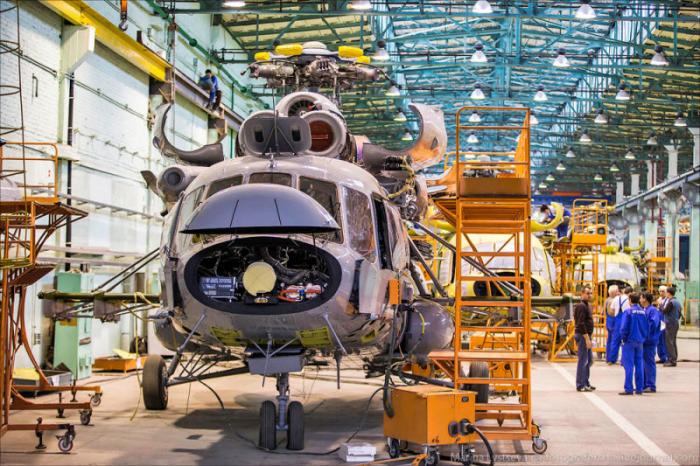
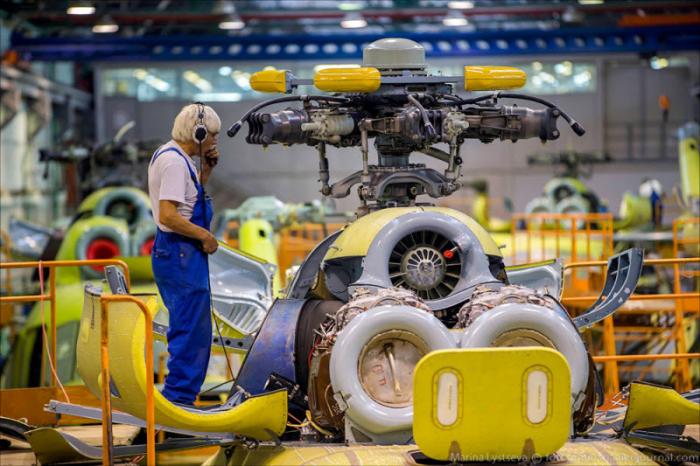
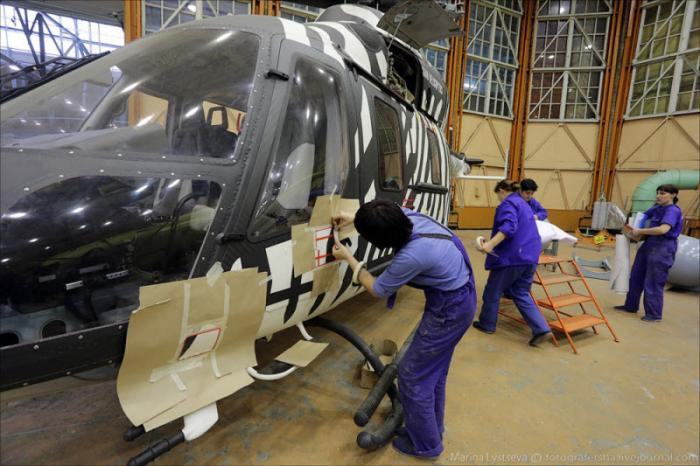
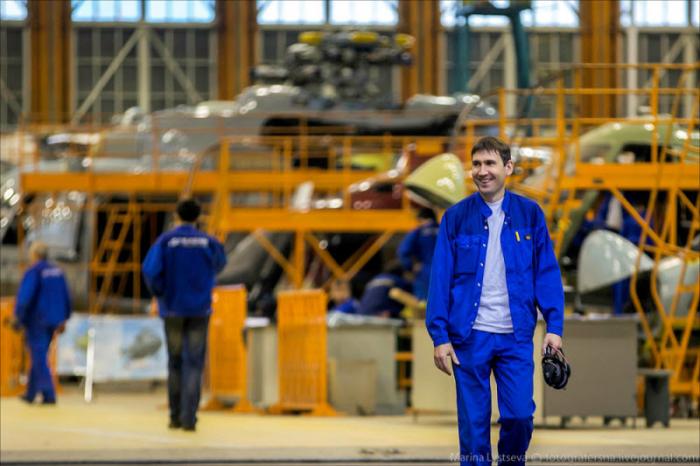
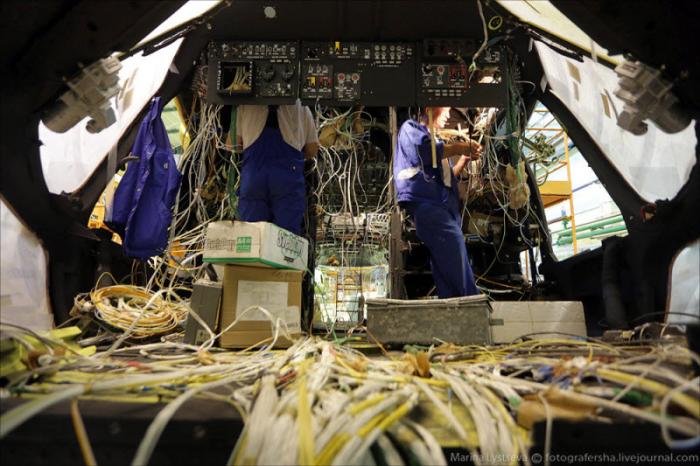
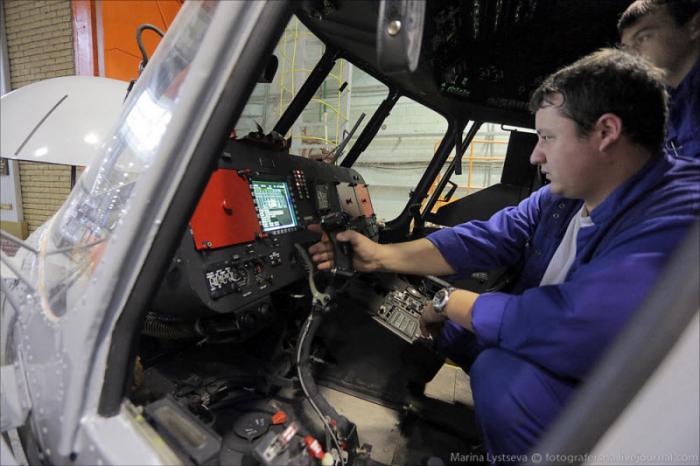
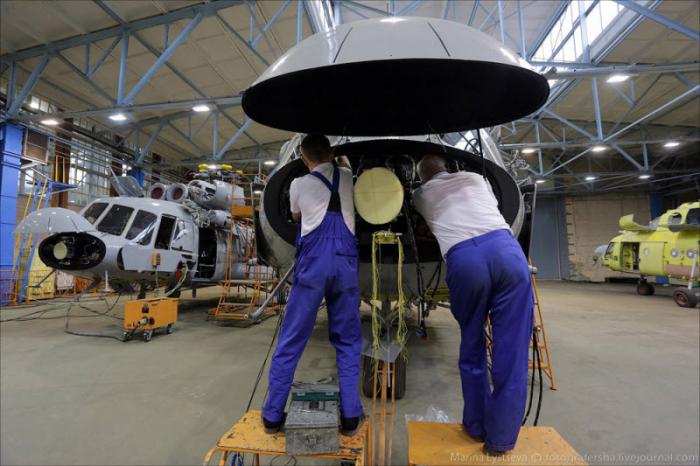
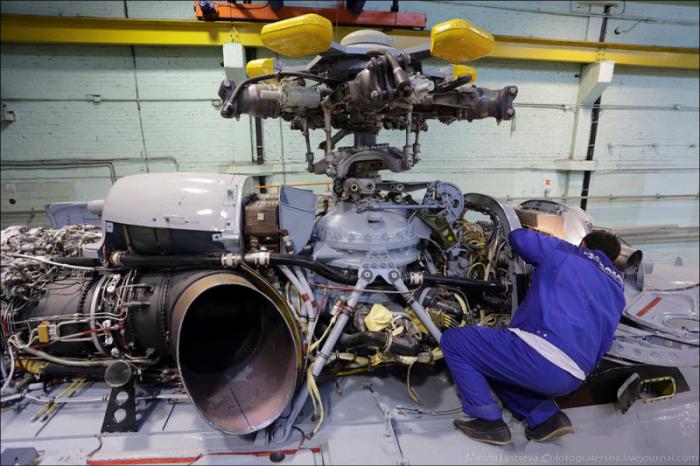
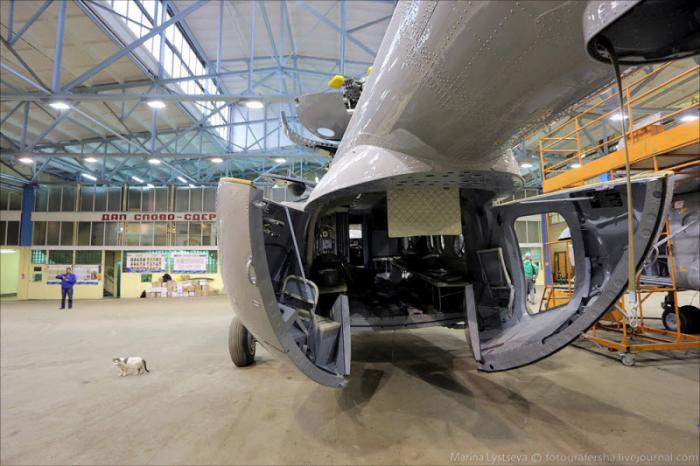
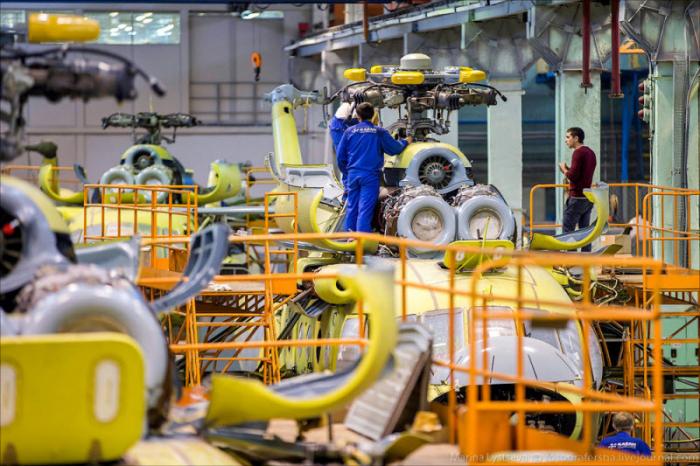
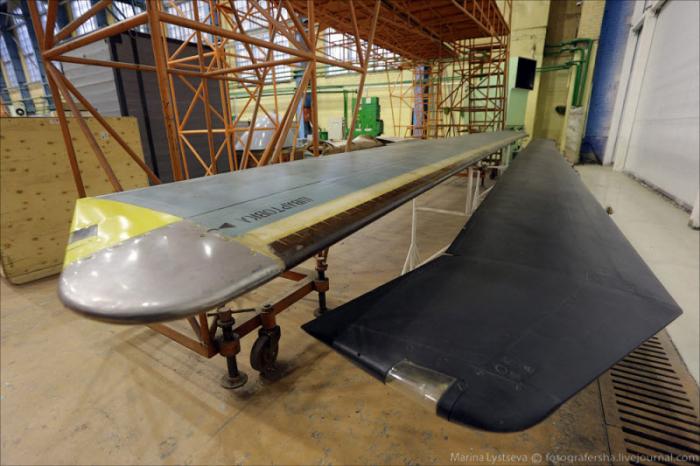
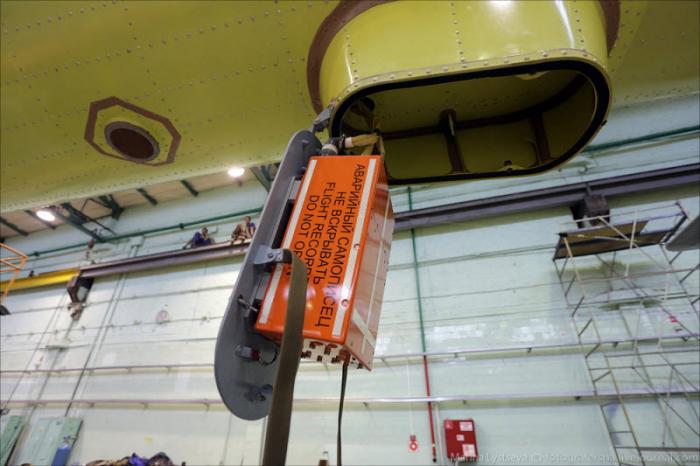
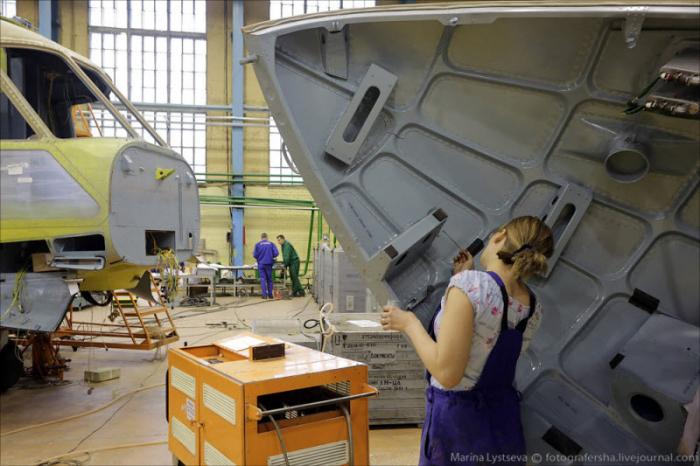
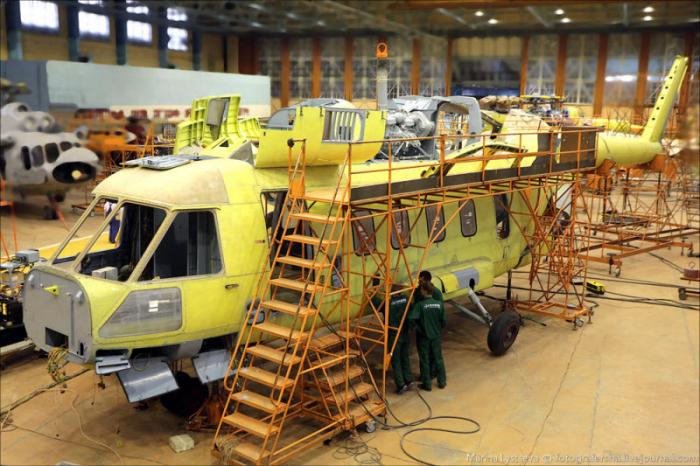
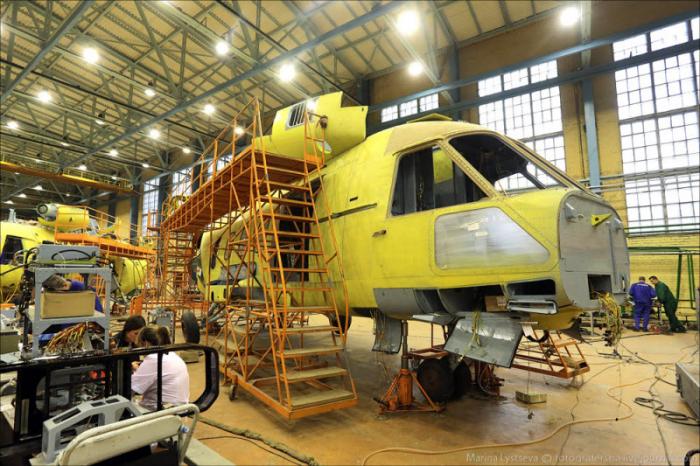
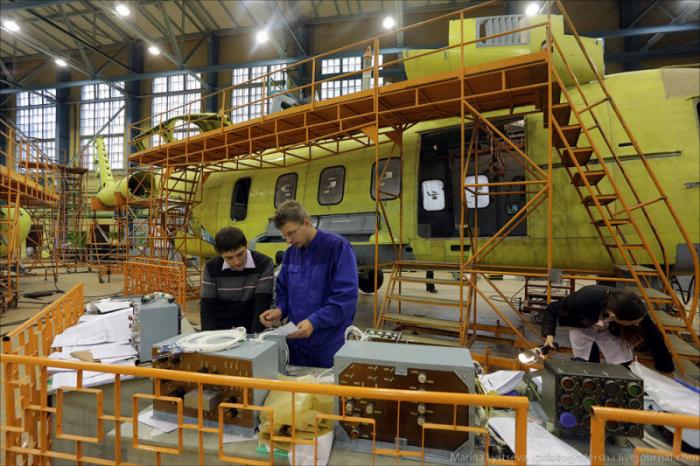
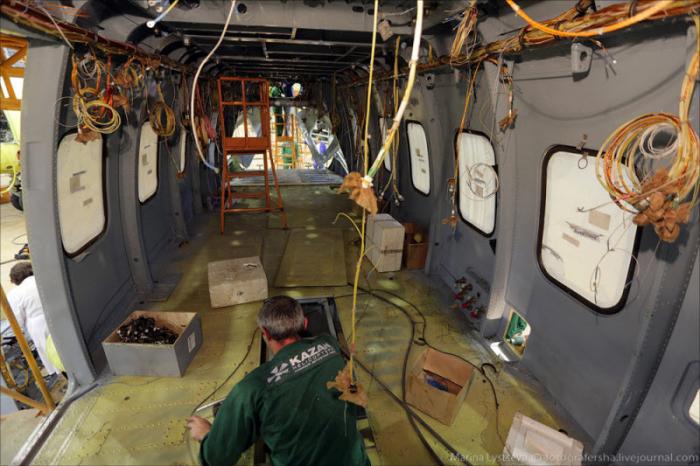
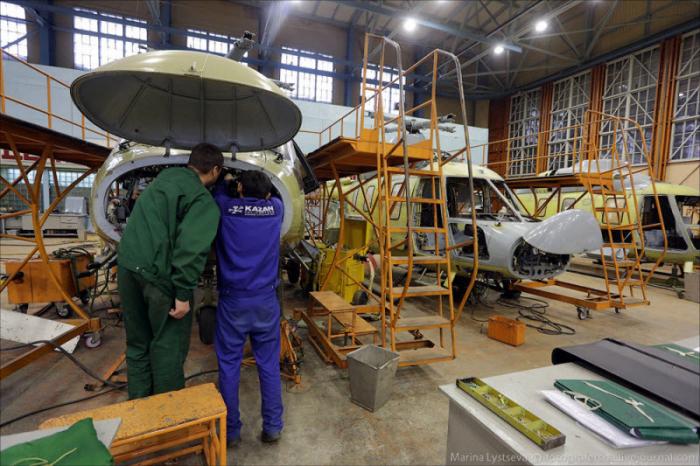
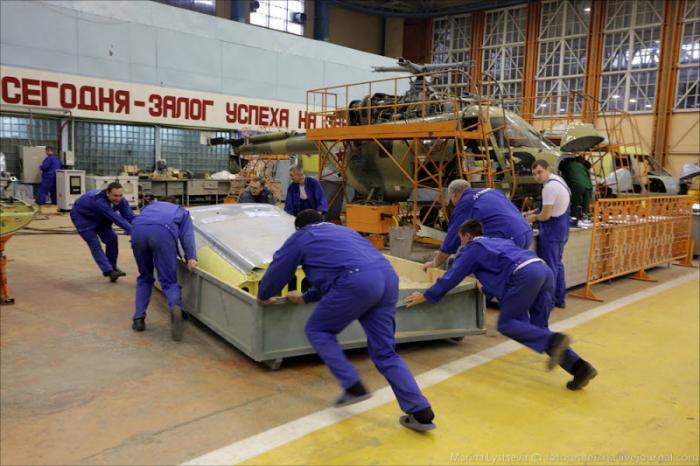
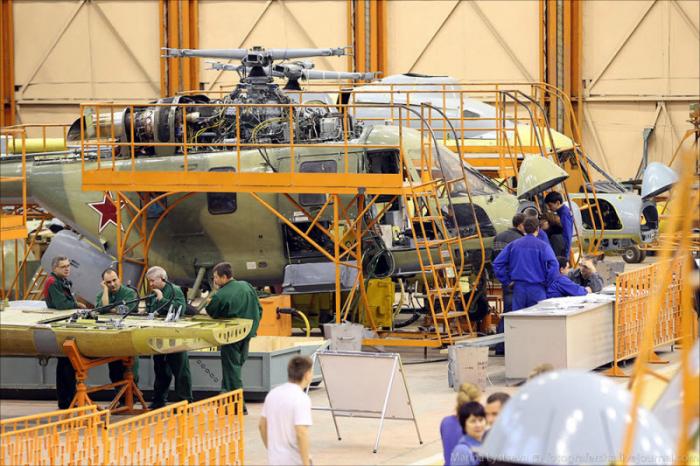
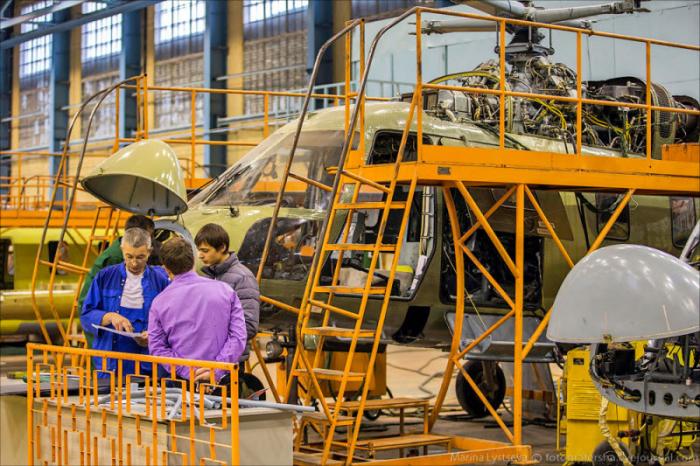
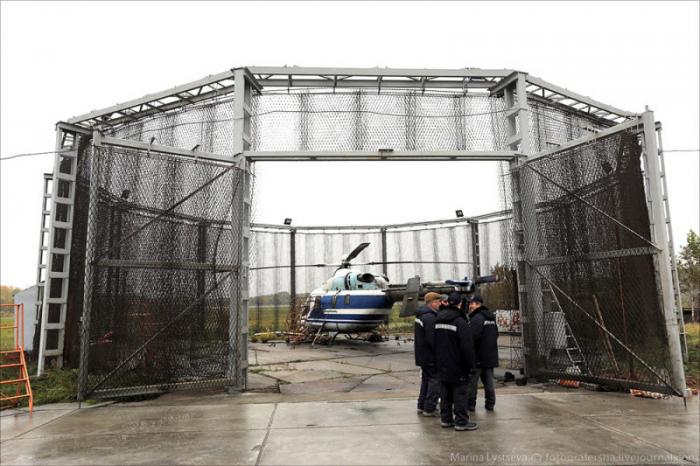
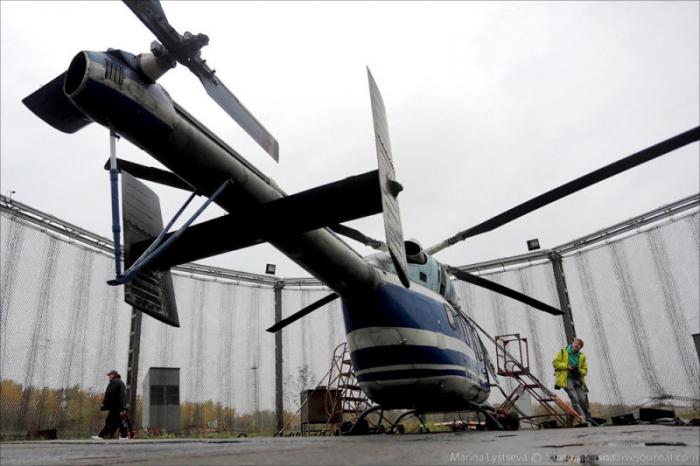
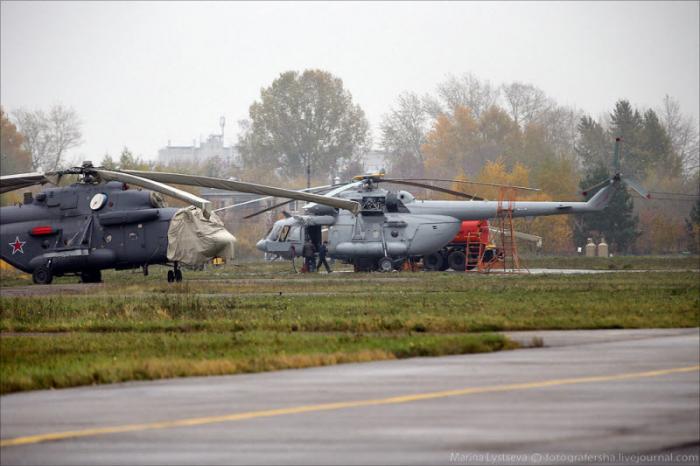
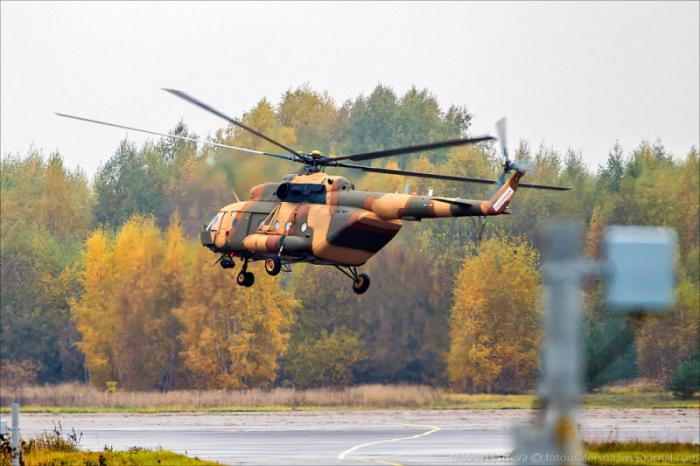
Авиационная судьба предприятия была определена в 1940 г., именно с этой даты идет отсчет истории нынешнего ОАО «Казанский вертолётный завод». В 1941 году легкие бипланы стали первыми воздушными судами, выпущенными заводом.
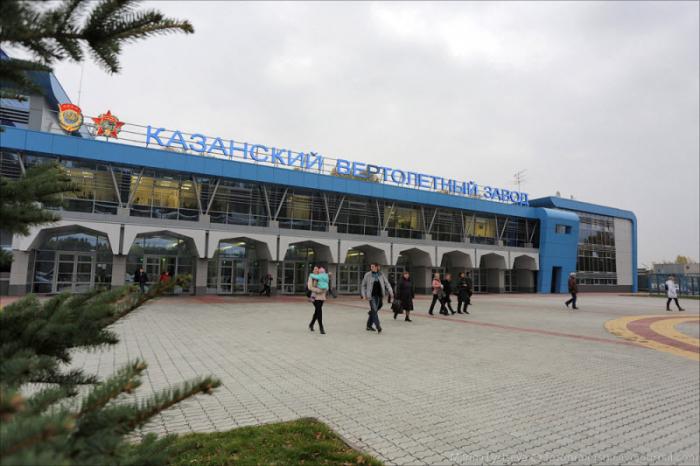
В 1956 году Казанский вертолетный завод начал поставки вертолетов на экспорт.
В 1965 году началось производство вертолета Ми-8. Это стало поворотной точкой в истории завода. Современный вертолет Ми-17 и его модификации - это результат огромного опыта, накопленного за время производства и эксплуатации вертолетов Ми-8.
Казанское вертолетное производственное объединение в 1993 г. преобразовалось в акционерное общество Казанский вертолетный завод, а в 1996 г. стало открытым – ОАО «Казанский вертолетный завод»
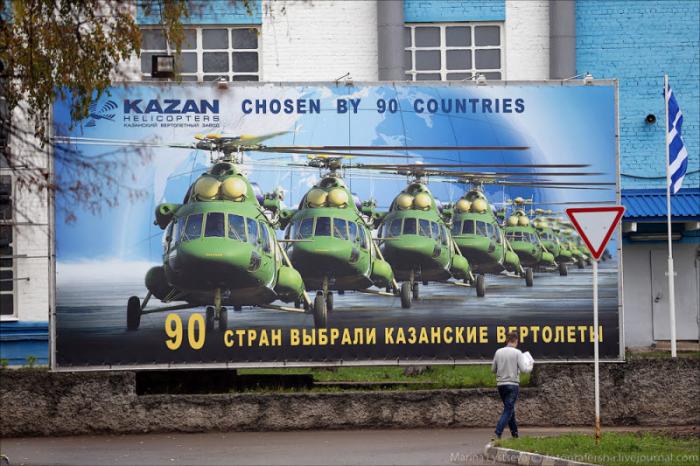
Производство вертолетов:
2006 - 53
2007 - 38
2008 - 58
2009 - 67
2010 - 81
2011 - 94
2012 - 103
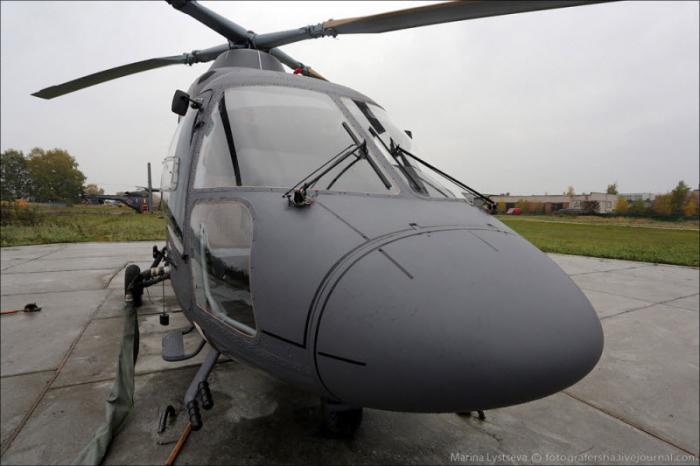
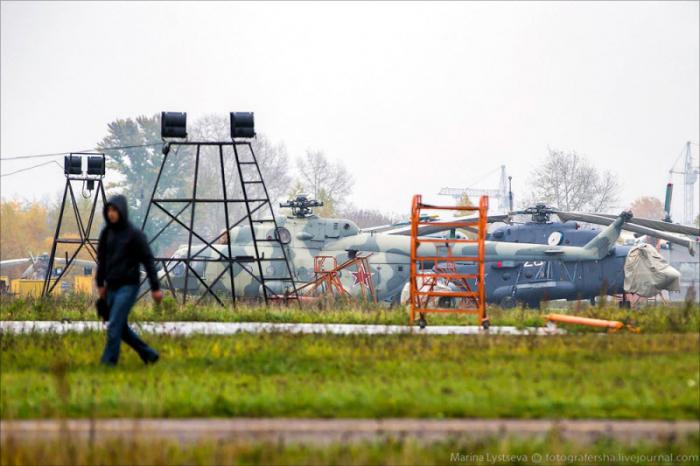
На сегодняшний день КВЗ остается самым большим в мире производителем вертолетов среднего класса.
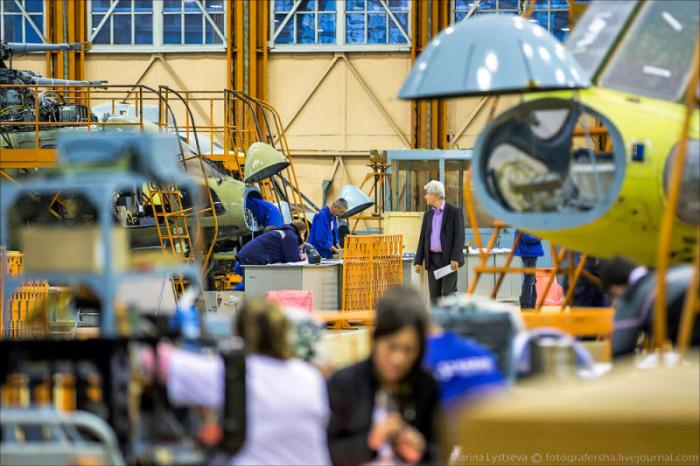
Традиционные для российского вертолетостроения рынки: Россия, страны СНГ, государства Юго-Восточной Азии, Африки, Центральной и Южной Америки. В настоящее время КВЗ поставляет технику примерно в 90 стран мира (продукция холдинга "Вертолетов России" в целом представлена более чем в 110 странах мира).
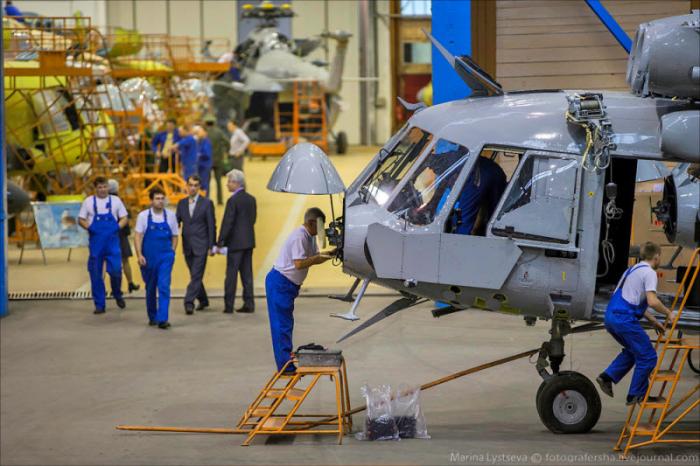
В этом году планируется достигнуть уровня свыше 100 машин в год при почти не изменившемся составе рабочего коллектива - около 7 тысяч человек со средним возрастом 36 лет (в цехах механического производства; по заводу средний возраст на сегодня – 43,2 года). И достигнуто это за счет реорганизации производства, которая началась в начале 2000-х годов с ремонта цехов.
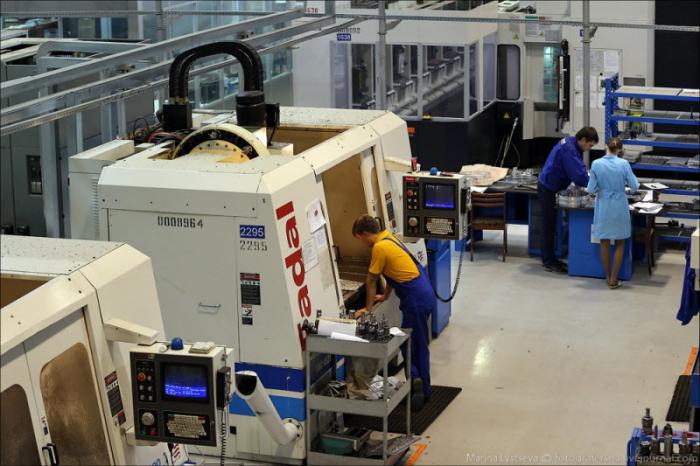
Не менее важный этап реорганизации предприятия последовал с закупкой нового оборудования в механообрабатывающее производство. Закупили станки иностранного производства, в связи с чем трудоемкость упала, а производительность труда выросла в 4 раза.
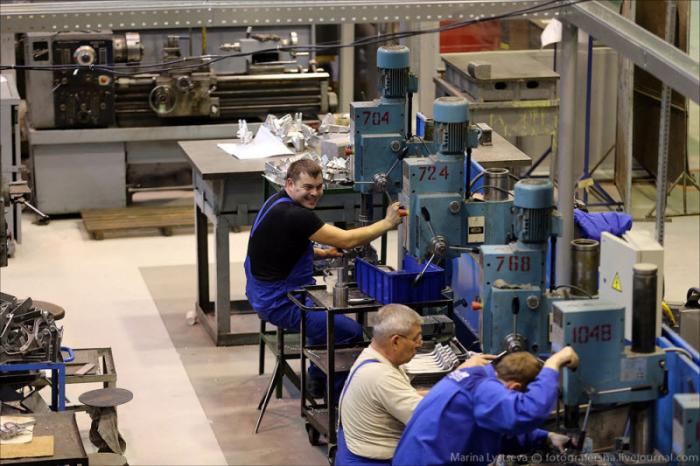
Шпангоуты сейчас обрабатываются на четырех трех- и пяти - координатных станках, которые заменили 24 старых (три линии по 8 станков каждая). Россия, к сожалению, пока не выпускает станков такого уровня. На фото – обработанная штамповка до покрытия.
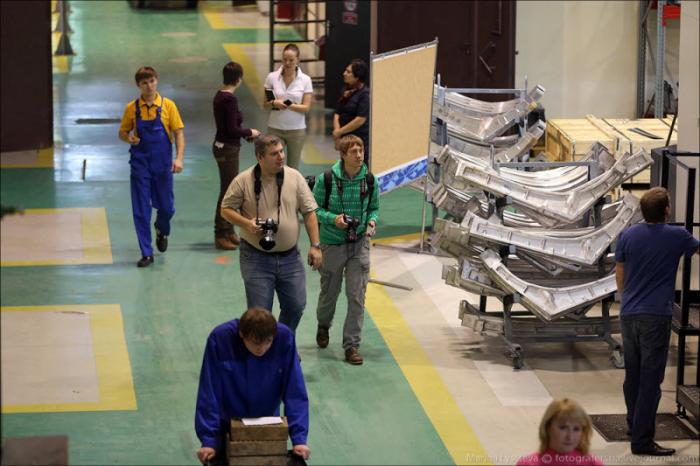
Готовые шпангоуты идут на дальнейшую сборку.
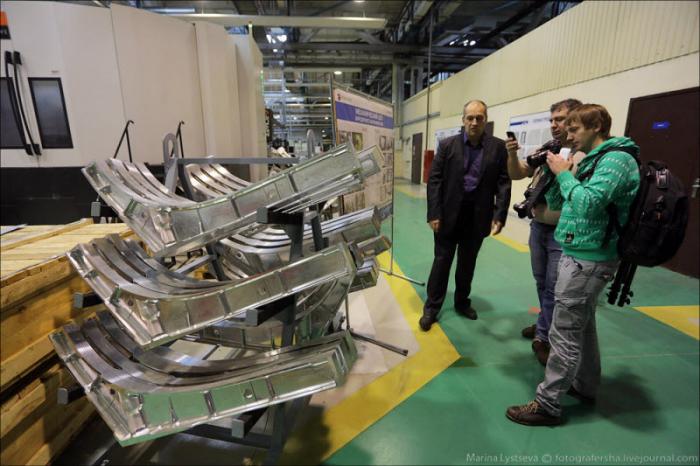
Деталь для автомата перекоса для "Ансата" раньше изготавливалась за 18 часов, а сейчас 12. Из-за обработки на нескольких станках брак составлял большой процент. Сейчас вся токарная часть, фрезеровка, сверловка осуществляются в рамках одного цикла. И так происходит со многими деталями.
На фото кольцевой шпангоут, который идёт на хвостовую балку на серийный вертолёт.
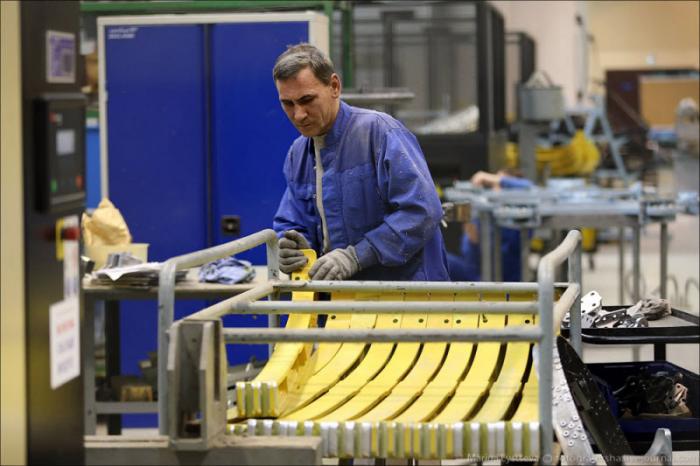
Ступица виброгасителя. Не каждый клиент ее заказывает. Раньше на изготовление этой ступицы уходило 136 часов, сейчас 18 - время сократилось почти в восемь раз!
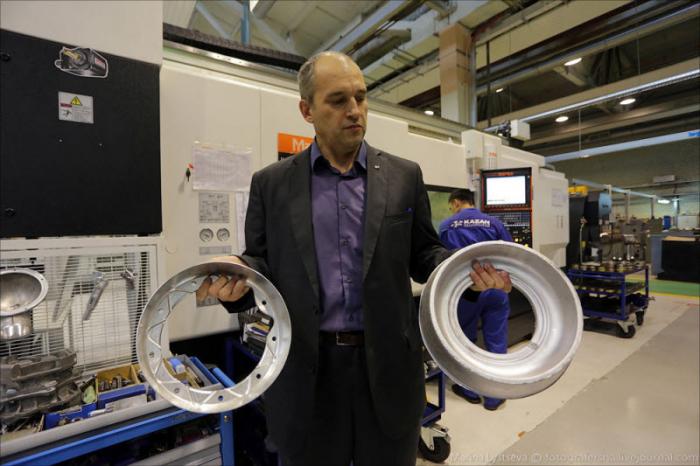
Служба главного технолога находится тут же в цеху за стеклянной перегородкой и не нужно ждать подолгу, как раньше, специалиста, пока он прибудет из другого корпуса.
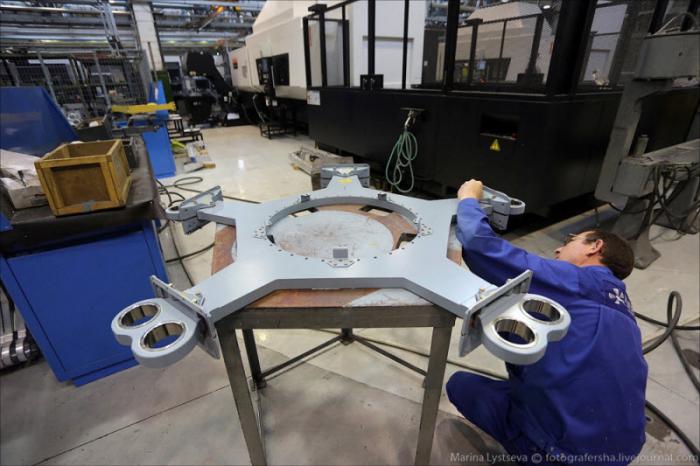
В цехе фрезерного направления работает 2 линии фирмы «Mazak». Одна (4 станка) обрабатывает легкие сплавы (дюраль), другая (3 станка) только сталь. Каждый станок имеет свой магазин на 120 инструментов, а на «стальной» линии ещё и магазинный центр на 240 единиц. Замена инструмента на «стальной» линии формируется автоматически – это заложено программным обеспечением.
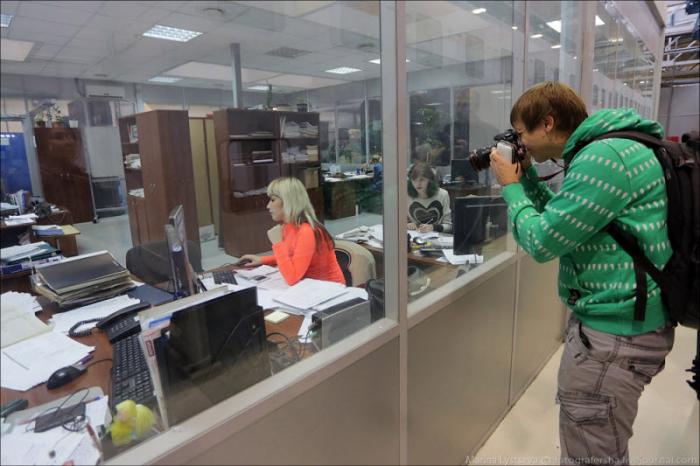
Допустим, у фрезы закончился ресурс, компьютерная программа сигнализирует о завершении назначенного ресурса, бегающая каретка забирает фрезу со станка, производит обмен и идет дальнейшая обработка детали. А оператор забирает отработавшую своё фрезу. Инструмент идет на переточку, его характеристики меняются и он идет на другое производство. Все инструменты с чипами, на которых записана история жизни детали.
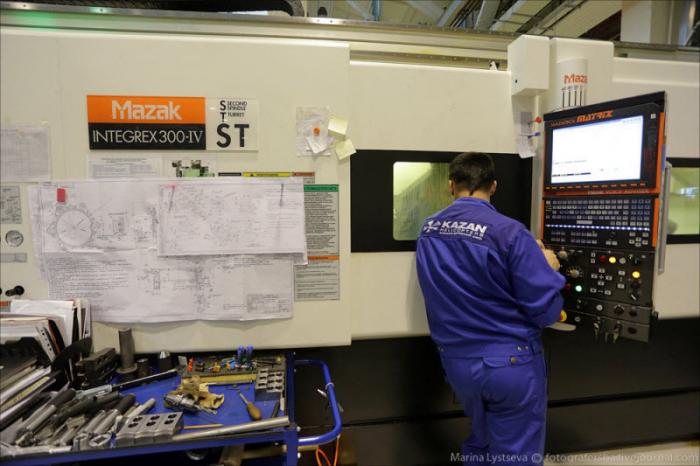
За время перестройки этот цех увеличил свою мощность более чем в три раза. Если раньше делали 6 тысяч нормо-часов, то сейчас план подходит к 21 тысяче, а с января 2014 будет ещё больше.
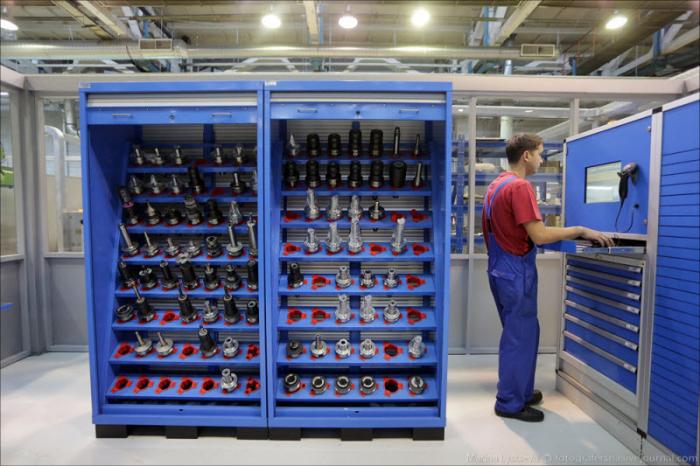
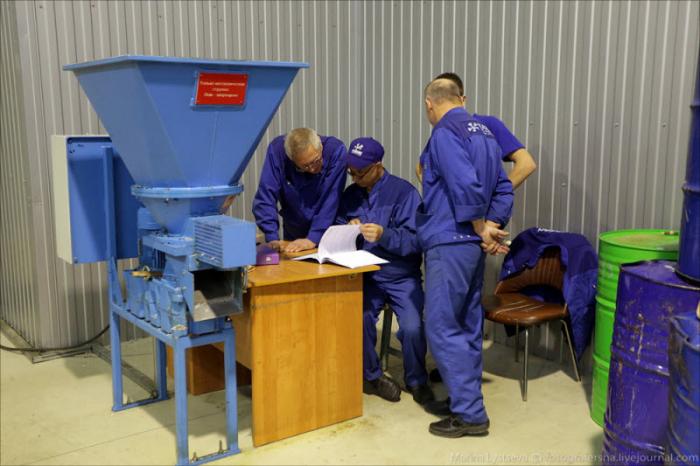
Раньше каждый день отсюда уходил груженый самосвал дюралевой стружки, сейчас отходов стало в 4 раза больше, но стружка превращается в удобные для транспортировки брикеты, которые после переплавки идут в другие виды промышленности.
Каждые 28 секунд из пресса выпадает дюралевый брикет. Каждые 32 секунды – стальной. Стоимость брикетов на рынке в 4-5 раз больше, чем просто стружка. Витую стружку утрамбовщик в брикеты делать не может, поэтому она попадает в «мясорубку» и после измельчения тоже занимает меньше места.
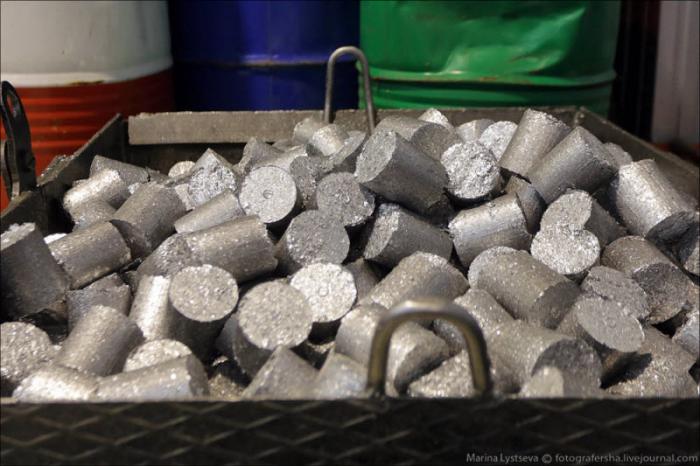
Экологическая защита. На заводе не водятся крысы и мыши. Репортаж Алексея смотреть у него на страничке.
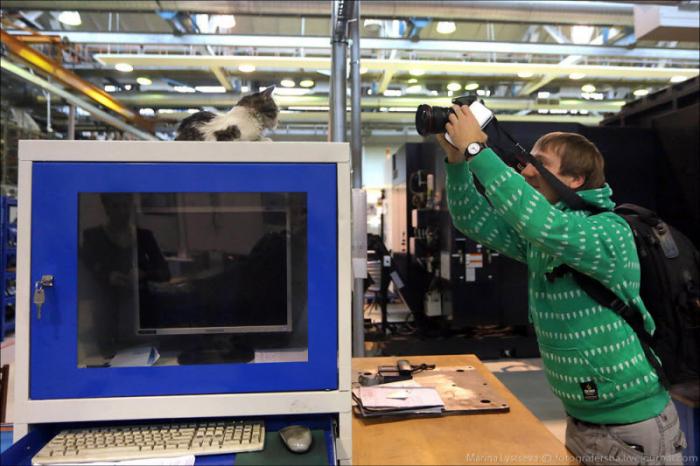
Чистота - залог экономического роста производства.
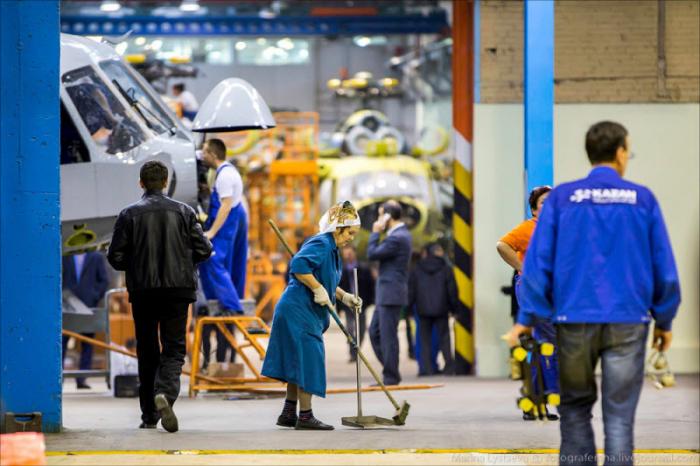
Перемещаемся в сборочный цех.
От начала сборки до первого полета вертолет находится тут в среднем один месяц, включая малярное производство.
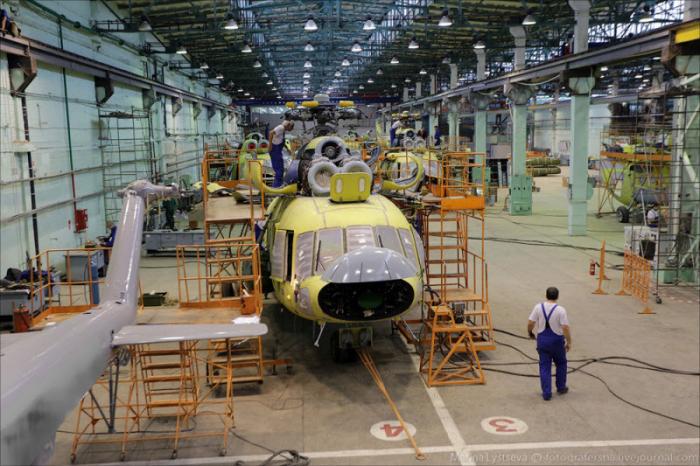
ОАО "Казанский вертолетный завод", входящий в холдинг "Вертолеты России", производит семейство вертолётов Ми-8/17, которые эксплуатируются более чем в 100 странах мира
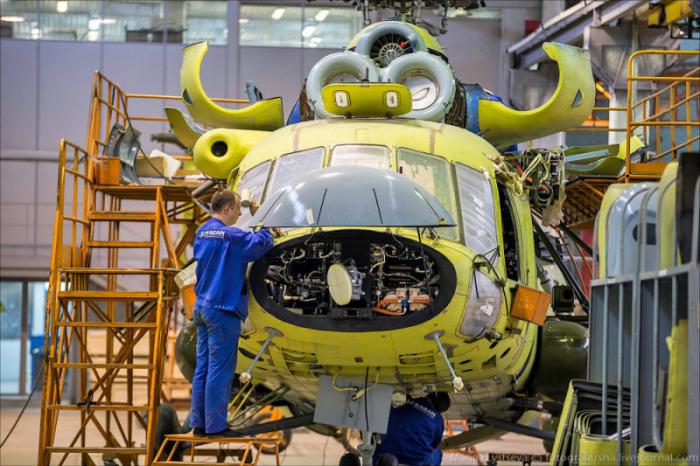
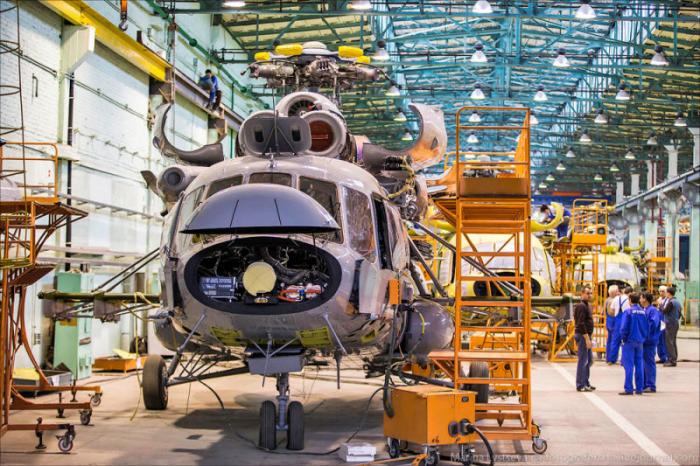
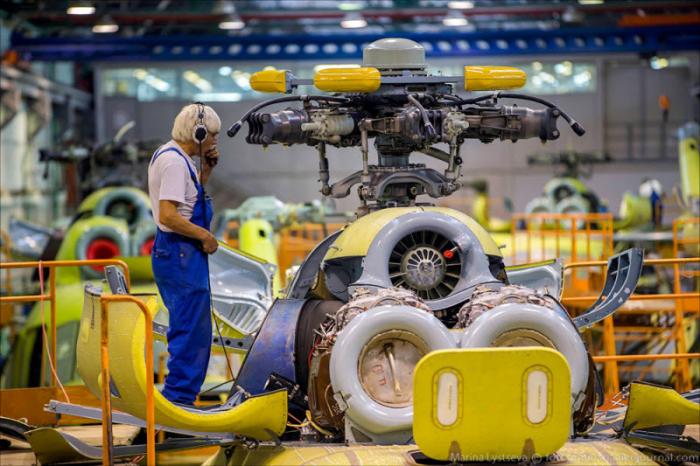
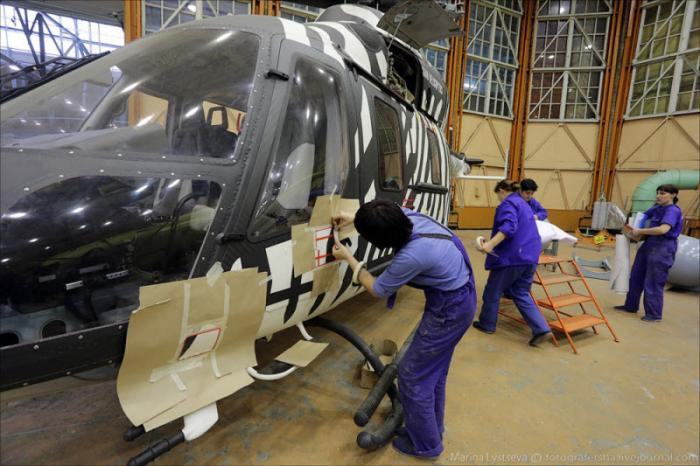
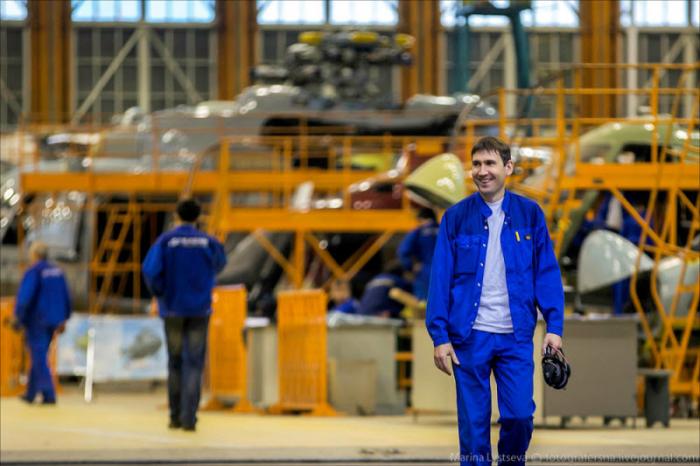
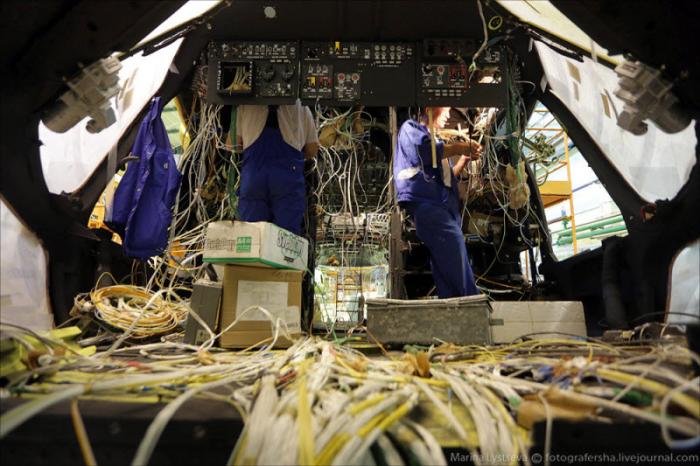
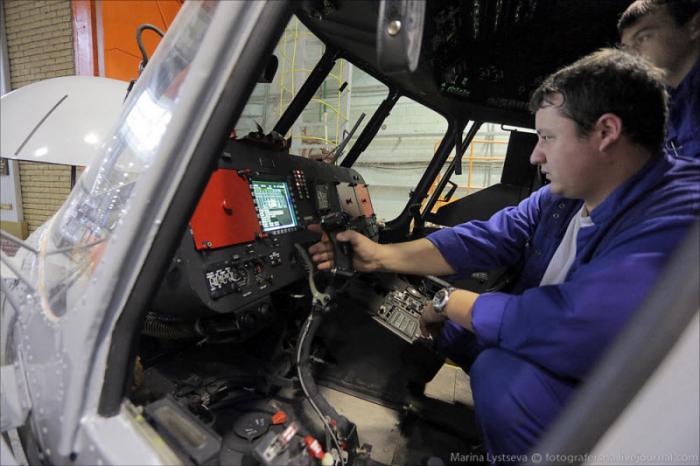
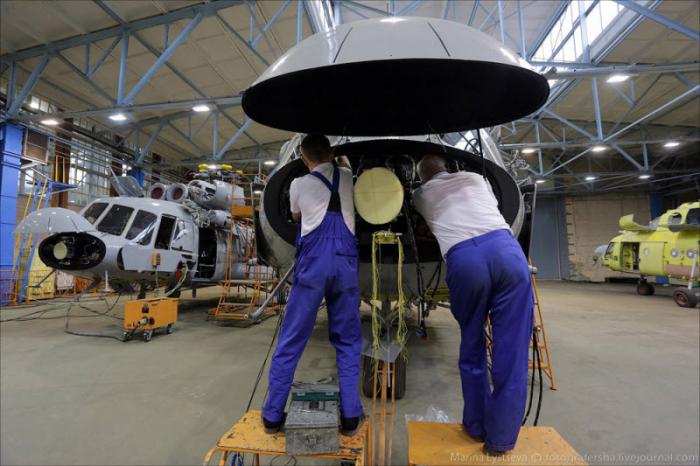
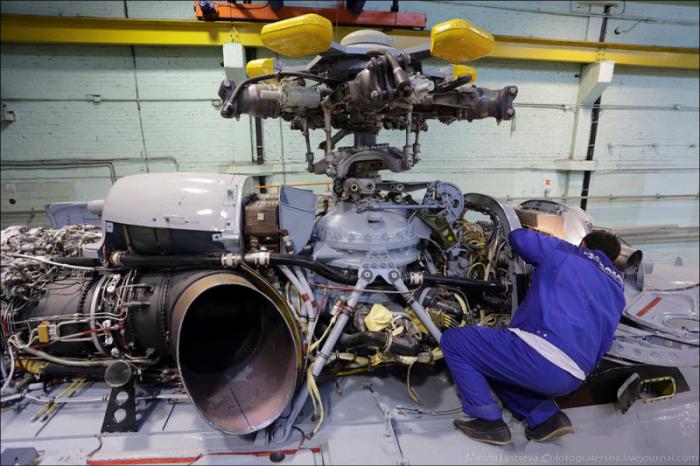
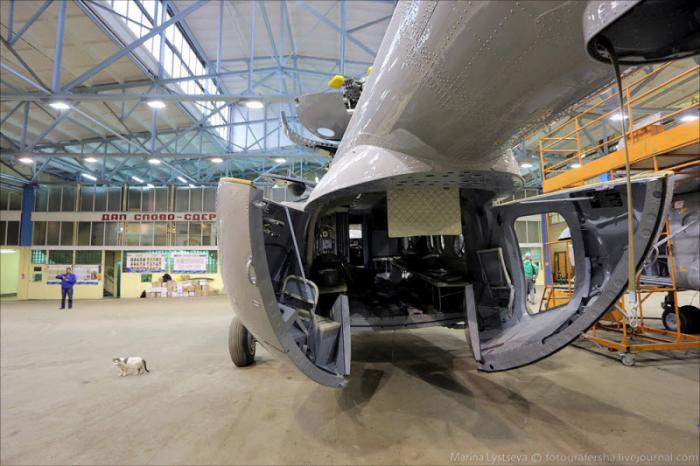
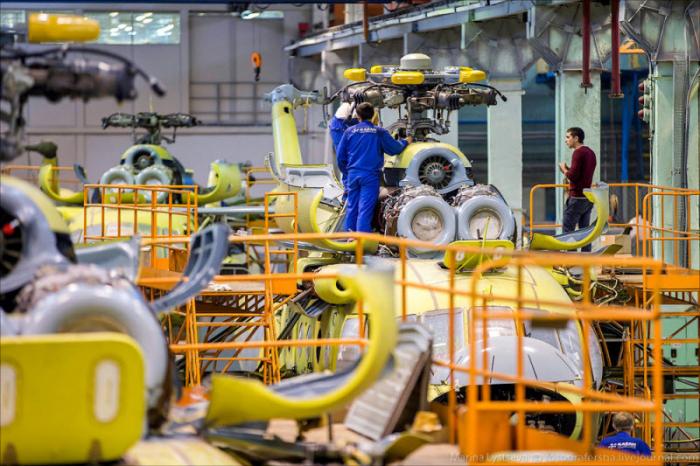
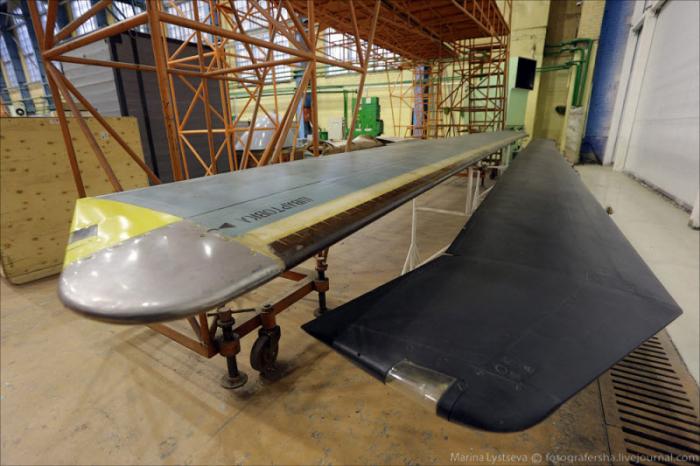
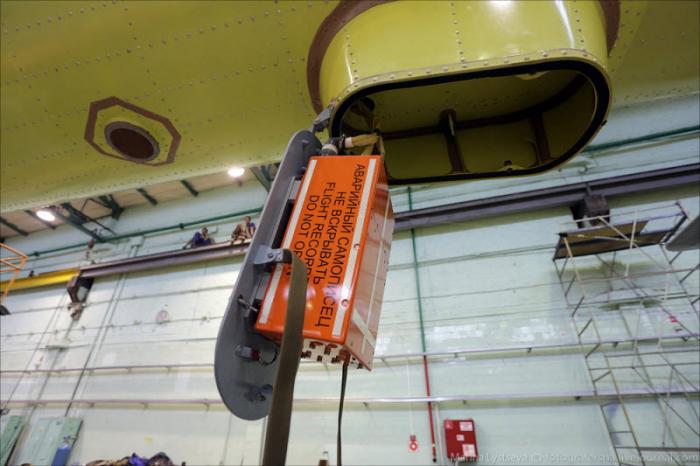
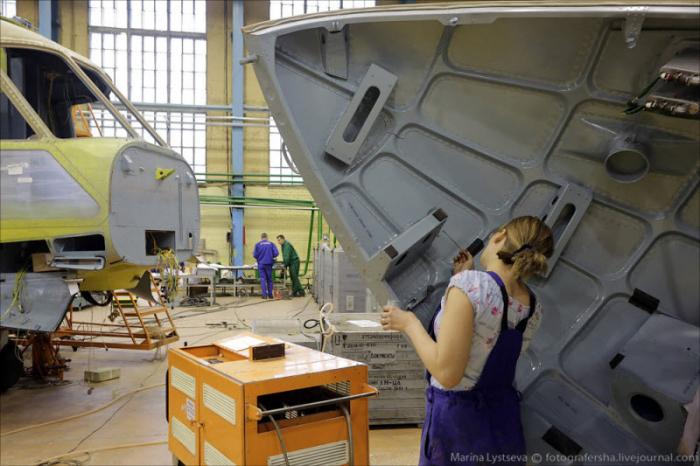
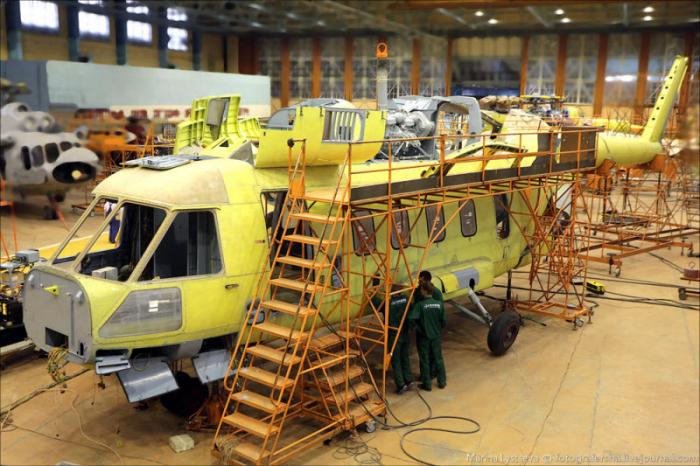
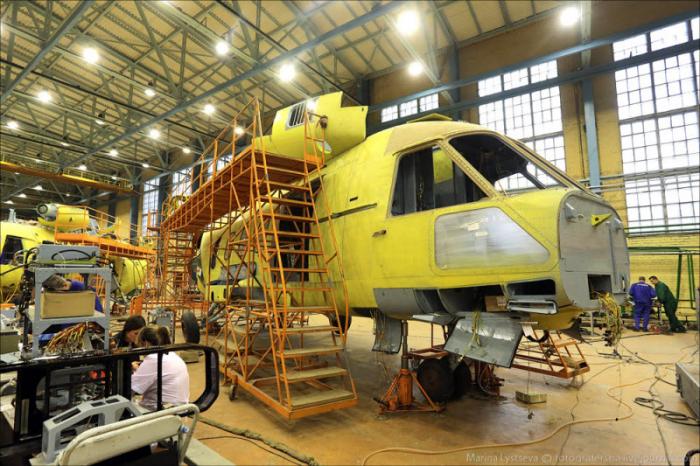
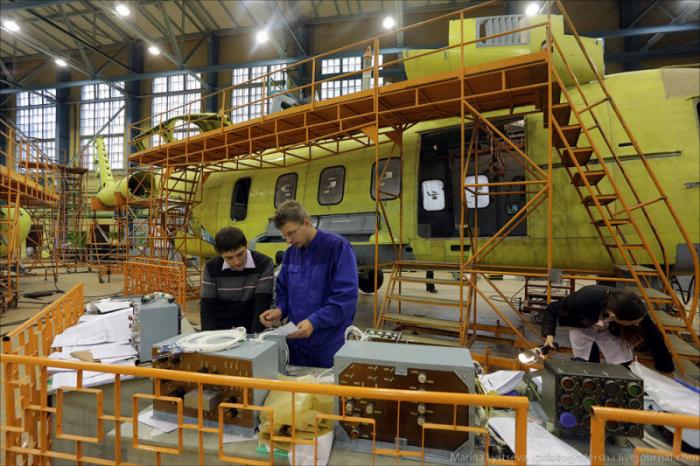
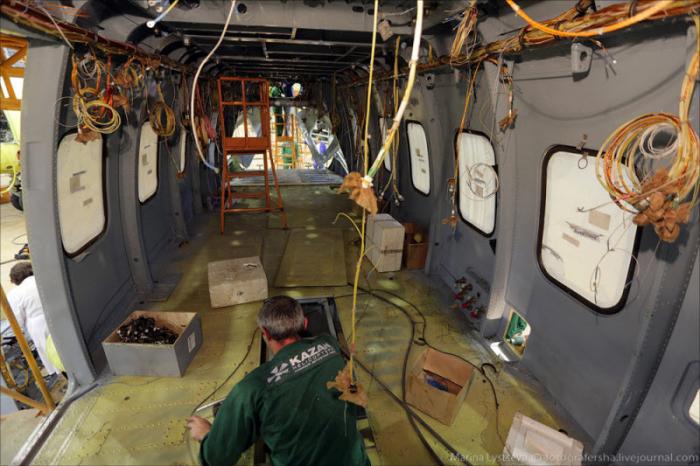
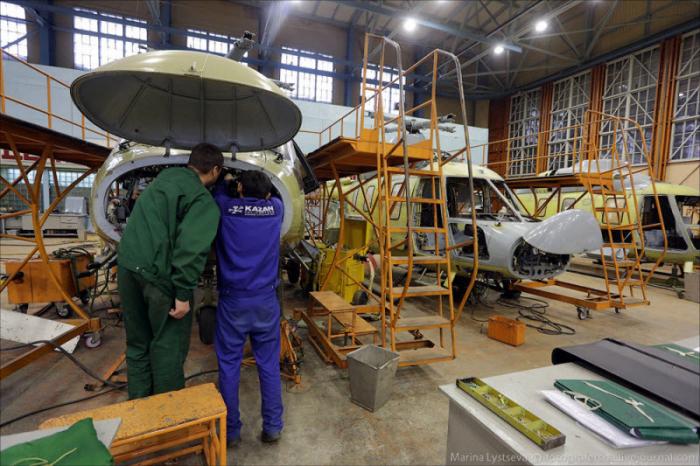
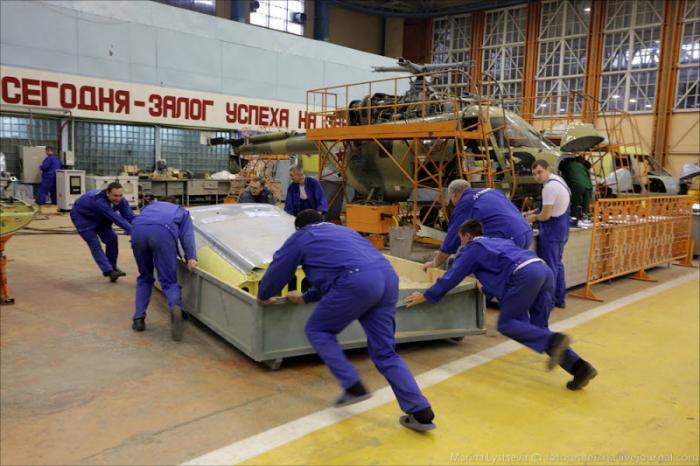
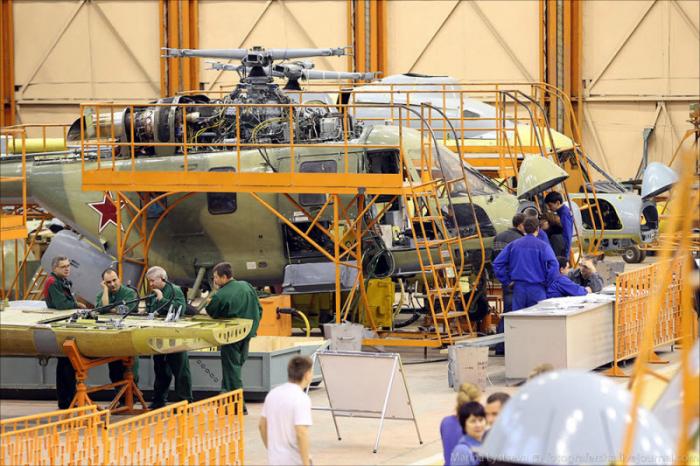
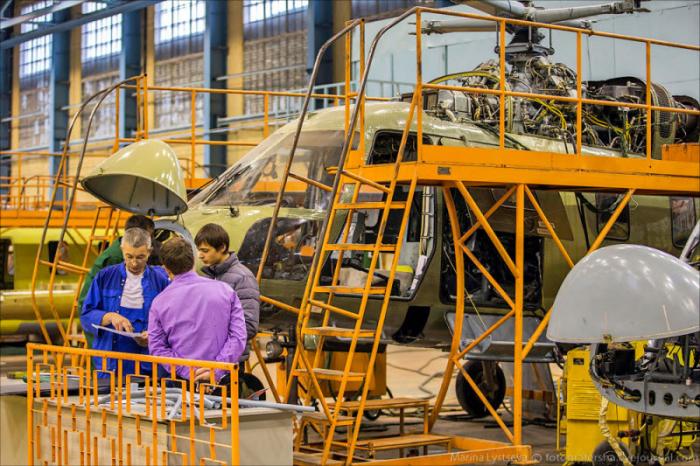
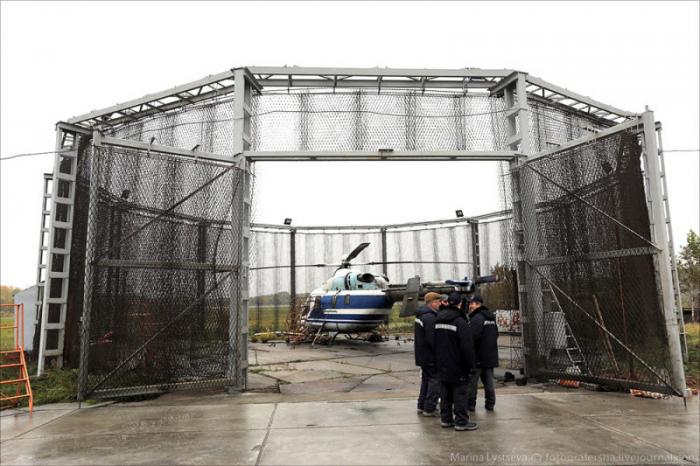
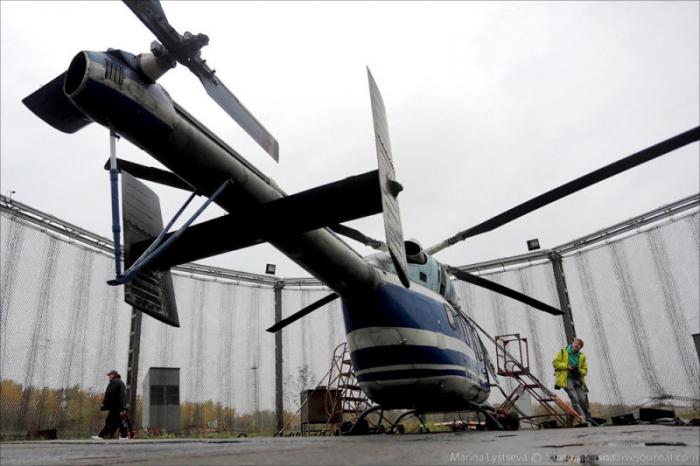
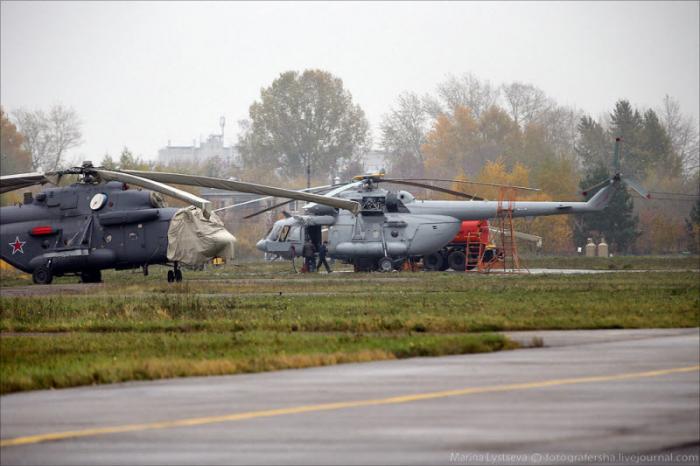
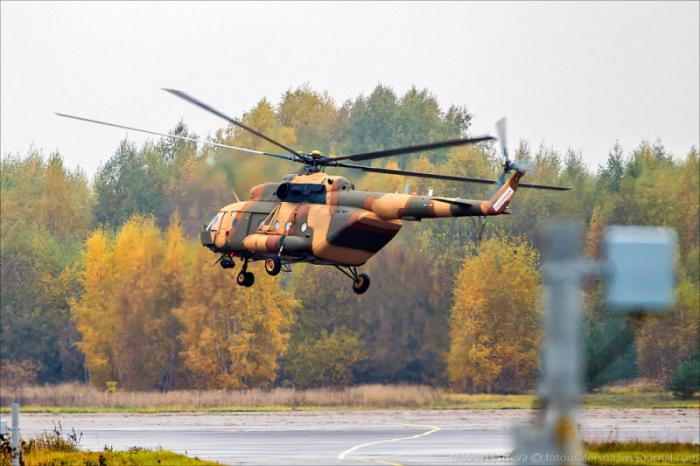
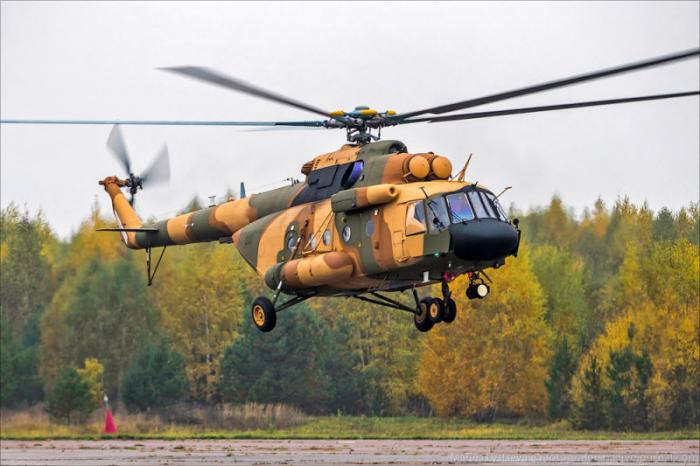
Похожие статьи:
Комментарии: